|
The Ken’s Carstar Project
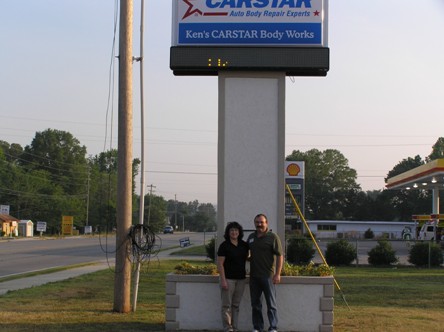
Owners Ken and Kyna White
-
Location: Dalton Georgia
-
14,000 square ft
-
Average 100 vehicle repairs per month
-
Production Employee breakdown: 5 body techs, 3 paint techs,1 frame tech, 1 mechanic,
-
Production support personnel: 1 parts tech,1 detailer tech,
-
Office staff: 1 receptionist, 1 estimator,
-
Ken and Kyna direct and support daily operations
A “Where do I begin and how do I get started” assessment concluded client needs and requirements.
-
A thorough 5 S production floor efficiency make over of the facility
-
A segmented system for the repair process of blue printing to included the tasks and duties of disassembly and reassembly in conjunction with parts receiving and staging for repair
-
Incorporate into the D&R (disassemble and reassemble) process the ability to fast track qualified repairs for expediency
-
Controlled material disbursement
-
Controlled fastener disbursement
New processing evolutions necessary to support client needs and requirements.
-
Revamp and train existing workforce to all process evolutions
-
Definitive parts procurement and distribution
-
User friendly parts receiving method, storage and transportation system
-
Parts tracking and staging for repair
-
Reduce material waste and redundant stocking through controlled inventory
-
Accurate production tracking of vehicles in repair
-
Set up the D&R area to enhance flow
-
Locate and create designated temporary holding areas for parts and equipment not immediately needed for repair
Production floor efficiency
Ken’s Carstar was an average repair facility with a definite need for reorganization on the production floor.
This needed transformation was more then Ken and Kyna could handle themselves as they tended to daily operations.
Yet they realized as owners confronting evolving industries trends and changing standards of operation was important to their business and had to be done.
The decision was made to outsource this task to A.P.S., a full service company that has the experience to renovate their facility with limited interruption to their daily production.
The next few slides will show before and after pictures of the facility makeover. |
|
|
5 S production floor optimization
Part of the 5S process is putting things in place so the tech has what they need where they need it. Keeping their feet in the stall working eliminates the need to search for equipment, tools and material. This methodology I refer to as" spoiling the tech” and it is an important step toward gaining the technicians buy-in as they soon realize the benefits of the 5S organization.
Paint Department
Body Shop
Body Shop
Body Shop
Body Shop
Body Shop
Frame & Mechanic Area
Frame & Mechanical
Frame & Mechanical
Outside
Autobody Production Services
As a full service consulting and implementation company “who we are is defined by what we do”. Our personal participation in thought, deed and action defines our willingness to work and sweat side by side with the production workforce to gain their respect and earn their trust. This creates an atmosphere conducive to accomplishing the goals of a 5S project and helps set the foundation for sustaining new processes and systems.
Actions Speak Louder than Words
New Processes and Systems
Part of the service we offer is the hands on production floor training of new processes and systems with the production employees. |
|
|
New Processes
Training Employees
Review: Ken's Carstar Project
-
Length of project: 14 days 101 hours
-
Achieved goals: Thorough 5S facility makeover
-
A D&R area fully equipped and staffed with fast track capability
-
100% Blue printing process
-
Parts check-in, storage and transport system operational
-
Production tracking system operational
-
Employee training on new processes completed
-
5S housekeeping rules in place
-
Material and fastener allocation operational
-
Bullpen holding area established
Read Ken's Carstar review about A.P.S. services
click testimonies / references
|
|